Bevel Gear Cutting Blade Geometry Inspection Pdf Scholar UPDATED
Bevel Gear Cutting Blade Geometry Inspection Pdf Scholar
Abstract
Recently, a new methodology for 5-axis flank calculator numerically controlled (CNC) machining, called double-flank machining, has been introduced (see "v-axis double-flank CNC machining of spiral bevel gears via custom-shaped milling tools—Part I: Modeling and simulation"). Sure geometries, such as curved teeth of spiral bevel gear, admit this approach where the machining tool has tangential contact with the textile block on two sides, yielding a more efficient variant of flank machining. To achieve high machining accurateness, the path-planning algorithm, however, does not await only for the path of the tool, merely likewise for the shape of the tool itself. The proposed arroyo is validated by series of concrete experiments using an annoying custom-shaped tool specifically designed for a detail blazon of a spiral bevel gear. The potential of this new methodology is shown in the semifinishing stage of gear manufacturing, where it outperforms traditional ball cease milling past an guild of magnitude in terms of machining time, while keeping, or even improving, the machining error.
Introduction
Efficient and highly accurate manufacturing of curved geometries such as car transmissions, gearboxes, or other doubly curved engine parts is a serious challenge in many industries like automotive or aeronautic, to proper name a few. Spiral bevel gears, when compared to straight-toothed bevel gears, are able to run at higher speed [1] and are therefore indispensable elements among gear mechanisms. To achieve polish and silent high-speed transmission, manufacturing with a very high precision is essential, e.1000., using directly face nanogrinding [2]. Moreover, high precision increases immovability of the manufactured gears that is another main objective for modern, sustainable manufacturing technologies [3].
Traditionally, manufacturing of spiral bevel gears requires specially deviced machines. In that location are several mainstream approaches to industry spiral bevel gears: gear hobbing with perimeter cut (Gleason) [four], cyclo-palloidal continuous generation past spiral hobbing (Klingelnberg and Oerlikon) [5], and continuous generation by spiral hobbing with conical-type cut (Klingelnberg) [1]. However, all these approaches are advisable for large manufacturing batches.
In contrast, the proposed approach aims at low-price manufacturing of a single workpiece and/or replacement of a broken part using five-axis computer numerically controlled (CNC) machining. The recent trends in gear manufacturing already head this management [6,7,viii], which is well-suited for minor batches and an economic alternative to the traditional approach using an expensive hobbing machine. At the same fourth dimension, CNC machining is able to keep loftier accuracy that is essential for gear manufacturing. Another significant advantage of five-axis CNC machining comes from the fact that information technology can exist combined with condiment manufacturing [ix]. This type of hybrid manufacturing enables, for case, gear repair, that is something highly desirable, but not possible with the traditional gear-cutting methods.
The purpose of this written report is to further advance the contempo geometric modeling simulations on v-axis CNC machining with custom-shaped tools [10]. That is, the path-planning algorithm does not merely expect for optimal machining paths, but as well for the shape of the tool itself [11,12,xiii]. While flank milling with curved (barrel) tools is known and possible for input free-form surfaces [10, 14] simultaneous tangential contact on ii sides requires a specific input geometry. The contempo numerical simulation results showed that for spiral bevel gears, a custom-shaped tool admits enough freedom to flank-automobile a curved valley betwixt ii screw gear teeth with a single sweep, having a bi-tangential contact throughout the motility. This newly introduced methodology, called double-flank, therefore offers fifty-fifty more efficient manufacturing than traditional flank machining. On a conceptual level, the tools used in this work are very similar to small grinding wheels [15,16,17], i.e., metal cores coated with abrasive particles [18, nineteen]. Therefore, the furnishings of the annoying grains on the surface accept to be taken into consideration.
In this paper, real machining experiments are conducted to physically validate the recently proposed double-flank machining methodology. The results show that this approach outperforms classical ball terminate milling by order of magnitude in terms of machining fourth dimension and, for the particular spiral bevel gear considered in this paper, this approach is well-suited for the semi-finishing stage. The results are also virtually compared confronting (unmarried) flank machining with on-marketplace barrel tools with favorable results for the proposed double-flank machining with custom-shaped tools.
Previous work
Manufacturing of screw bevel gears has been studied over several past decades, see, e.m., [1, 4, 5, 20] and other relevant references in [20]. The whole loop: design, production, inspection and installation of spiral-toothed bevel gears is a complex process that requires a special handling. There are several geometric constraints that need to be satisfied to guarantee polish transmission between the cutting tool and the textile block: (i) the flank contact betwixt the conjugate gear pair (the tool and tooth) has to be along a whole line (curve), (ii) the line contact is equally distributed in the unabridged engagement expanse, and (iii) the line contact needs to preserved at every instant of the motion [four].
Traditional pipeline for manufacturing of gears is aimed for large batches and groove-making machines that rely on slotting on curved tool. The ii main approaches: the continuous indexing method, referred to equally "face hobbing", and the single indexing method referred to equally "face milling" nowadays some differences. The face hobbing method produces an epicycloidal shape in tooth lengthwise management. The face up milling method is processed in such a way that both flanks are manufactured in a unmarried cut, i.e., a constant slot width results in the tooth root due to the circular cutter head [21]. While palloid gears are produced by a conical hob, the cyclo-palloid gears are manufactured using a confront hob cutter.
This paper belongs to a family of modern approaches that focus on gears manufacturing using universal multitasking machines or five-axis milling centers [22, 23]. The principal advantage of this new trend stems in its versatility as the tool in general does not depend on the gear geometry. This fact makes the technology very flexible every bit it tin can exist performed on various milling centers, and non, in contrast to the traditional methods (Gleason and Klingelnberg), on one specific large-calibration machine.
Suh et al. [8] use a 3-axis milling automobile with a rotary table; yet, ball end milling is applied in semi-finishing and finishing stages. A numerical approach for determination of car-tool settings for roughing of a pinion past using a spread-blade confront milling cutter is proposed in [three]. Five-cut method is applied and the manufacturing time is minimized past maximizing the material cut during the rough-cutting phase. Traditionally, standard tools are frequently used for gears machining in universal machining centers [7]. However, this newspaper follows the recent tendency where free-grade tools are used for near-to-net-shape machining, especially for complex slots, such as the tooth infinite of the gear.
For certain type of gears, such as non-circular spur bevel gear, the irregular shape makes the design and manufacturing procedure even more than difficult and forging stage is involved to distribute the material according to the shape features of the gear [24]. Another issue that needs to be carefully considered is surface roughness. A model to predict and control the teeth surface roughness for 3 + two axis milling using brawl end milling has been proposed recently [25].
Other recent works accept focused on gears machining with universal machines using milling technology [26, 27]. Nonetheless, innovative processes with higher material removal rates are i of the master objectives in modern manufacturing. In this line, Super Abrasive Machining (SAM) [28] is one versatile and feasible solution that increases gears' machining efficiency. Specifically, SAM provides grinding technology precision [29] with like machining feeds and costs, just with shorter machining times.
This research goes in the direction of efficient spiral bevel manufacturing using universal multitasking machines or v-centrality milling centers, where the main objective is to further reduce machining time. To this end, the proposed research aims at the semi-finishing stage using highly efficient double-flank machining where not only the path of the tool, but also the shape of the tool itself are the unknowns in an optimization-based framework.
The remainder of the paper is organized as follows. Department 3 gives a brief summary of the mathematical derivation of the custom-shaped tool pattern and its 3D motion. Section 4 describes the instance study and Section 5 shows the results obtained. Finally, Section 6 discusses the hereafter research directions and concludes the paper.
Double-flank machining and custom-shaped tool blueprint
The basic edifice blocks of the double-flank machining algorithm will be briefly recalled, more details tin be constitute in [xi]. The proposed approach starting time initializes the movement of the tool using a bisector surface of the tooth space and estimates the initial shape of the tool (Section 3.i), followed by global tool and motion optimization (Section 3.2).
Initialization of double-flank machining
The goal is to approximate the space between ii teeth of a gear Φ, recall Fig. 1, past an envelope of a full general tool Ψ such that at that place is a bi-tangential contact between Φ and Ψ on both sides of the molar space (double-flank machining). The unknowns in an optimization-based algorithm are both the machining tool Ψ and a ruled surface R (the movement of the tool's centrality). The ruled surface is represented equally a (3 × 1)-tensor product B-spline patch
$$ R(t,s) = (i-s)\mathbf{p}(t) + s \mathbf{q}(t), \quad [t,due south] \in [0,1]\times[0,1], $$
(1)
where s is the parameter in the management of rulings and t is the time parameter of the ii purlieus cubic B-spline curves p(t) and q(t), for more details encounter [xi].
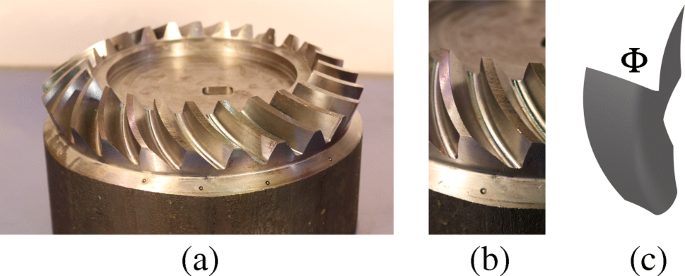
(a) Spiral bevel gear (5-axis CNC machined using the proposed methodology). (b) A zoom-in to i molar space (aka "valley") between two teeth and its CAD model that is formed by a doubly curved complimentary-class surface Φ (c)
Given the valley Φ between two teeth of a gear, first the bottom part of the valley is trimmed off (as this part cannot be flank-machined anyway). This trimming operation defines two side surfaces Φ1 and Φ2. As the machining tool is aimed to have tangential contact with both Φ1 and Φ2, the bisector surface B is computed. The bisector, nevertheless, is a general surface, and therefore spline fitting method is used to compute its ruled surface approximation, see Fig. 2(b).
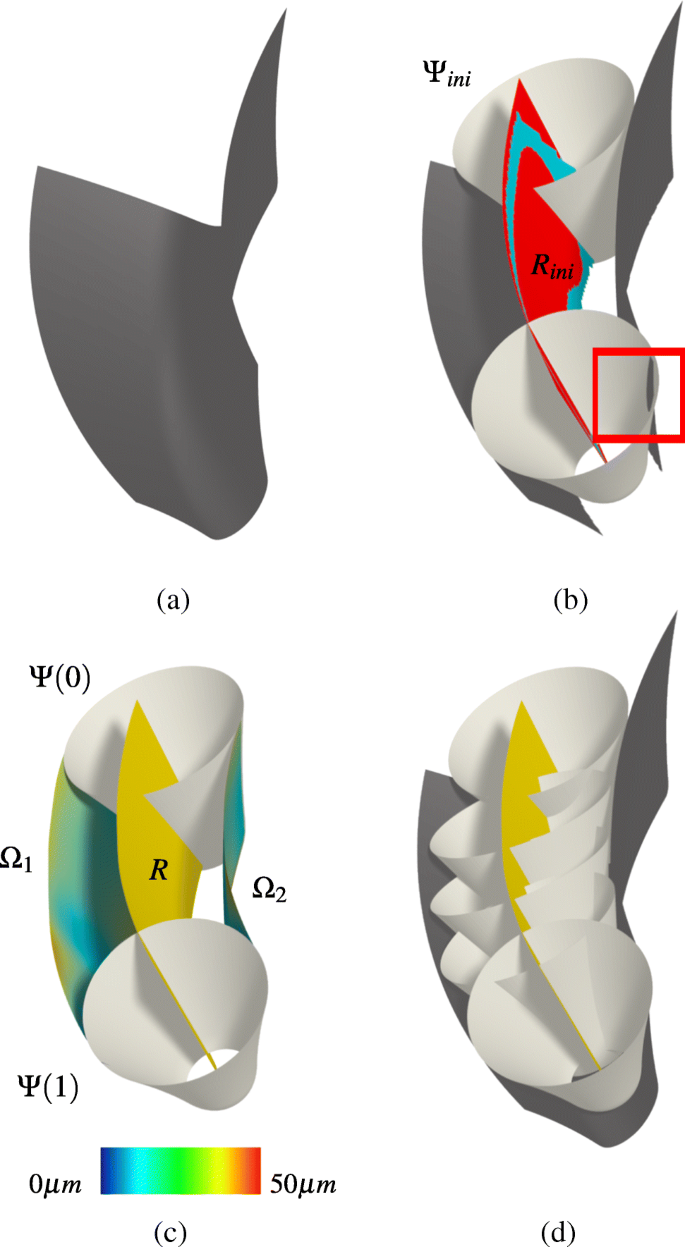
Blueprint of the custom-shaped tool. (a) A cavity bewteen two teeth represented as a spline surface. (b) The self-bisector B (blue) is fitted by a ruled surface R i northward i (red) and an initial shape, Ψ i n i , of the tool is computed. The initial tool and its initial position may penetrate the reference surface (framed in red). (c) The tool Ψ and its trajectory R both undergo global optimization to minimize the fault of the left (Ω1) and correct (Ω2) envelopes from Φ. The envelopes are color-coded by the distance error dist(Φ i −Ω i ), i = 1,2, that meets fine machining tolerance of 50 μm. (d) The concluding double-flank motion of the custom-shaped tool Ψ through the gear valley
The initial ruled surface defines the initial shape of the machining tool Ψ and its envelopes define the initial approximation of the two surfaces Φ1 and Φtwo. The two (right and left) envelopes Ω1 and Ω2 are required to guess Φ1 and Φii, respectively, as shut every bit possible, and within the given machining accurateness ε = fifty μm, see Fig. 2(c).
To compute the best envelopes Ω1 and Ω2, it is formulated as an optimization problem. The unknowns are the two curves p(t) and q(t) (boundaries of the rule surface R) and a scalar function d(s) that determines the sphere radius in the ruling management s. To compute the self-bisector B of Φ, the motion of the tool is conceptualized as a two parameter family of spheres (one in time, second in the ruling management) that should ideally impact Φ on two sides, see Fig. two(b). B is and then a locus of all such centers of spheres. The right and left sides (defined past trimming off the lesser part of the valley) surfaces Φi and Φ2 are used, see Fig. 2(b), to compute B, and and then
$$ F(\mathbf{z}) = \text{dist}(\mathbf{z},{\Phi}_{1}) - \text{dist}(\mathbf{z},{\Phi}_{ii}), $$
(ii)
where \(\mathbf {z} \in \mathbb {R}^{3}\) is the desired center of the sphere and dist is the point-surface minimal altitude. The iso-surface F(z) = 0 that defines the bisector B is computed using a variant of the marching cubes algorithm, see [xi] for more details.
Tool and motility optimization
In the proposed optimization-based framework, both the tool Ψ and its motion, represented by a ruled surface R, are optimized. The optimization has two main objectives: (i) to judge the surface within a fine machining mistake, i.e., remove as much cloth as possible and (ii) to guarantee that the envelope of the tool lies inside the valley Φ, i.e., there is no overcut.
Every bit discussed in Section 3.i, an initial ruled surface R i n i is computed from the self-bisector B. This gives also, for each value of s, s ∈ [0,one], a set of scalar values that correspond to the distance dist(R(t,s),Φ) and past averaging these values for various t one obtains an initial radial function d ⋆(s). This gives an initial pair of envelopes \({\Omega }^{ini}_{1}\) and \({\Omega }^{ini}_{2}\). However, these envelopes, in general, intersect Φ which corresponds to overcutting, see Fig. 2(b).
To eliminate this phenomenon, the tool Ψ i n i and its motion R i n i both undergo global optimization. The goal is to optimize them such that \({\Omega }^{ini}_{one}\) and \({\Omega }^{ini}_{2}\) become as close as possible to Φ (remove as much material every bit possible) and they both lie within the valley (no overcut). To achieve this goal, we proceed every bit follows. The ruled surface R is uniformly sampled both in t and southward parametric directions to obtain r i j := R(t i ,s j ), \(i=one,\dots , g\), \(j=i,\dots , northward\). In our discrete approach, for each s-parameter value (stock-still j), one obtains a ready of detached values d i j which are the distances from Φ for a fixed point of the axis as it moves in time. To obtain a motion of Ψ that is penetration-free with Φ (no overcut), we define
$$ \underline{d}_{j} = \underset{i=1, \dots, m }{\min} d_{ij}, $$
(3)
where \(\underline {d}_{j}\) are the penetration-free radii. In this detached setup, the penetration-costless radius depends on the sampling density. m = 100 was set up in all the experiments; this value turned out to be sufficiently large to render stable values for the valley shown in Fig. 1.
These radii are the lower bounds of the signal-surface distance for each j, i.east., distances that define (discrete) radial function that corresponds to a penetration-complimentary tool, run across Fig. 2(d). Consequently, the penetration-costless error is defined as
$$ \varepsilon_{j} = d^{\star}_{j} - \underline{d}_{j} $$
(4)
where \(d^{\star }_{j} \) are the samples of the initial radial part d ⋆. Denote past d a vector of unknown distances \(\mathbf {d}:=(d_{1},\dots ,d_{northward})\) and optimize both, the ruled surface R and d.
Finally, the objective that at every time instant t the tool is required to exist equally close as possible to Φ, but likewise penetration-free, is formulated. This leads to a minimization problem
$$ \brainstorm{assortment}{@{}rcl@{}} F_{\text{prox}}(\mathbf{p},\mathbf{q}, \mathbf{d}) = \frac{1}{mn} \sum\limits_{j=1}^{n} \sum\limits_{i=1}^{m} \left( \text{dist}(\mathbf{r}_{ij},{\Phi}) - d_{j} - \varepsilon_{j}\right)^{2} \rightarrow \min \end{array} $$
(5)
subject to the axis-rigidity constraints
$$ F_{\text{rigid}}(\mathbf{p},\mathbf{q}) = \langle\mathbf{p}(t_{i}) - \mathbf{q}(t_{i}), \mathbf{p}(t_{i}) - \mathbf{q}(t_{i})\rangle - Fifty^{ii} = 0, $$
(vi)
where dist(,) is a bespeak-surface distance and L is the length of l. The unknowns in the minimization are the control points of the two B-spline curves p(t) and q(t), and the vector of sphere radii d. m = 100 and northward = thirty was fix in the numerical simulations. More details on the whole tool-optimization process can be plant in [11].
Example study
The results of the path-planning algorithm described in [11] were converted into a CL-file, and consequently converted into a G-code, and tested in a conventional machining center, Kondia HS1000, see Fig. 3. The semifinishing operations were carried out with both a ball cease tool and a custom-shaped tool. The custom-shaped tool was capable of bi-tangential machining, which resulted in a simultaneous semifinishing of both walls of the molar space. One of the objectives was to reduce machining times in the semifinishing stage every bit the custom-shaped tool admits broad strips of high accurateness and therefore merely a unmarried path is needed, in contrast to brawl end milling which requires many milling paths.
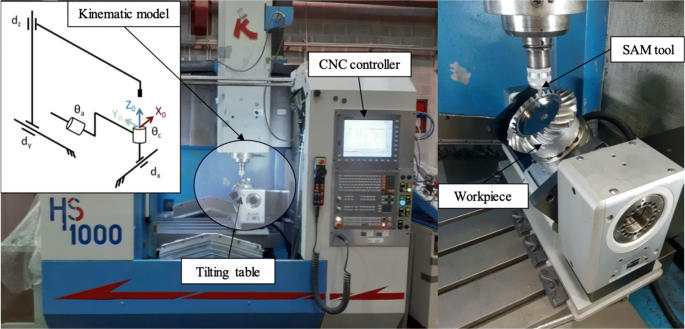
5-axis milling center
Spiral bevel gear was selected as a example written report equally it is i of the virtually widespread components in the industrial sector. It is as well the element par excellence used to transfer power from ane element to another, by transmitting circular move in terms of the gear wheel contact. Ane of the well-nigh important applications of gears is the manual of movement from the shaft of a power source, such as an internal combustion engine or an electric motor, to some other, end-effector, shaft. In either case, a loftier accurateness is highly demanded as the machining errors influence significantly the performance.
The gear wheels tin exist manufactured from a wide variety of materials to obtain the correct mechanical properties. From the bespeak of view of mechanical blueprint, force and durability, i.e., wear resistance, are the most important attributes. In full general, the gear designer should consider the power to manufacture the gear, from the formation of the gear teeth up to the final assembly of the gear in a auto. Other considerations include weight, corrosion resistance, noise, and cost. F-1550 steel (18CrMo4) was selected every bit the testing cloth for manufacturing of the spiral bevel gear, since information technology reaches a adequately proficient understanding with all the characteristics that steel needs to possess. Mechanical and physical properties and chemical composition of the used materials are shown in Table one.
This particular spiral bevel gear was chosen, because its contact surface is larger compared to those of straight-toothed bevel gears, and this fact poses a great challenge when computing both the tool geometry and the machining path. The specific characteristics of the bike and the theoretical mating pinion for a five/3 gear ratio are shown in Table 2.
The tests were carried out on a conventional machining eye, Kondia HS1000. This machine is a 5-axis milling motorcar, with 3 linear and 2 are rotary axes. The linear axes are 2 in the head (X, Z) and one in the table (Y), while both rotary axes are in the indexing tabular array (A, C). The spindle speed capacity is 24,000 rpm.
Initially a 210-mm-diameter and 120-mm-thick steel billet was used as a starting betoken. A series of previous operations were carried out to achieve a geometry close to the concluding. These operations are shown in Fig. 4 together with machining times needed for each particular machining phase.
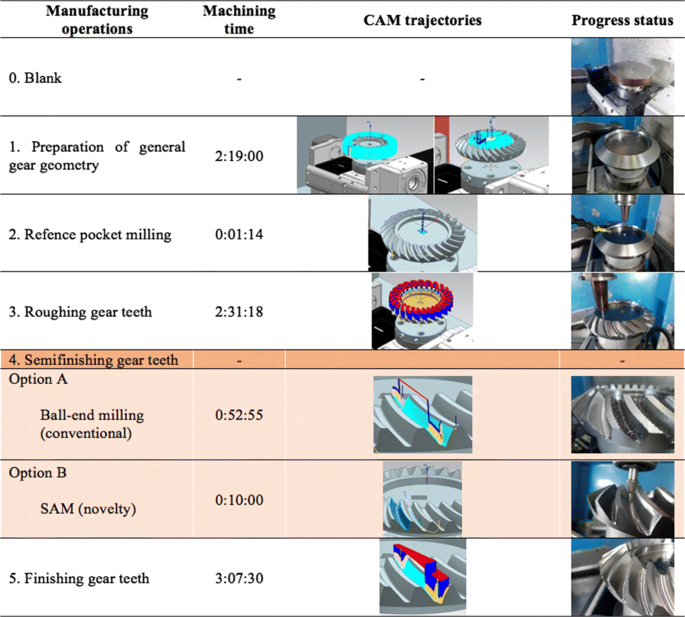
Progress and machining time summary of the whole gear manufacturing process. The machining time is formatted every bit hours:minutes:seconds
Custom-shaped tool for SAM
Regarding the SAM tool, a custom-shaped tool was used to perform the semifinishing operation of the tooth space. Its coat was a monolayer electroplated CBN grinding with a grain size of 300 μm, see Fig. 5. A tool of this type was chosen due to its excellent tool wear characteristics, because the abrasive grains are resharpened as they break up during the machining process and too considering the SAM process is well adapted to the calculation and manufacturing of a custom-shaped tool. When manufacturing the tool core, the thickness of the binding cloth and the abrasive grains were taken into account in order to obtain a tool with the exact geometry calculated in the modeling stage. The radius of the tool varies from 4.8 to xiii.2 mm, see Fig. 6, and the thickness of the abrasive coat is 0.5 mm. Note that the tool has negative Gaussian curvature (i.due east., it is not a conical tool), come across [11] for more detailed analysis on the tool blueprint.
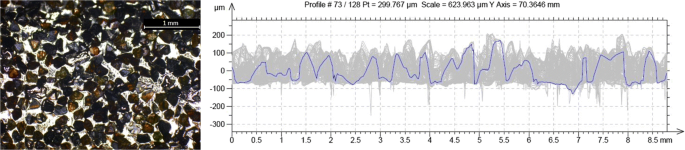
Grain distribution and profile
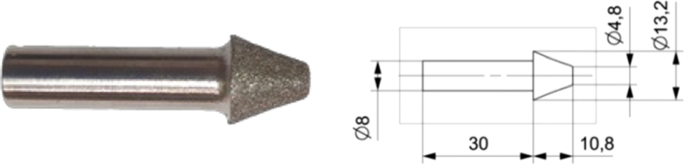
Custom-shaped grinding tool and its geometry
Concerning cutting weather, these were adapted towards the SAM technology in this sort of machining centers, in particular they were adjusted to the spindle capacities, with a spindle speed of 24,000 rpm, the limit of the machine, and a feed rate of 250 mm/min. It is important to note the effect of cutting speed on machining, particularly in the context of super abrasive machining. The optimal SAM conditions of the speed of rotation should be around 60,000–90,000 revolutions [31]. However, to achieve these speeds, high operation heads are required which conventional machines do not have.
Results and validation
To physically validate the results of the modeling algorithm, the machining path of the custom-shaped tool in the manufacturing of a spiral bevel gear was practical. More specifically, the custom-shaped tool was used in the semifinishing operation, which is the place where Super Annoying Machining engineering science has its potential niche of piece of work. In Fig. 7, the valley between spiral bevel gear teeth is shown during roughing and semifinishing operations with milling and SAM operations. Find a clearly visible difference in the quality of surface smoothness in Fig. vii(a) and (c).
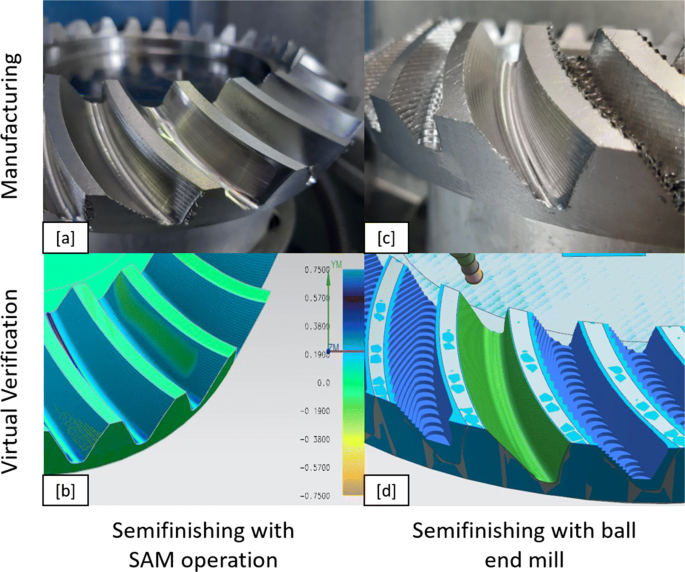
Spiral bevel gear semifinishing performance. (a) Manufacturing with SAM. (b) Virtual verification with SAM. (c) Manufacturing with ball stop factory. (d) Virtual verification with ball cease mill
A qualitative comparison between double-flank machining using a custom-shaped tool and ball terminate milling, during the semifinishing phase, is presented. Moreover, a virtual comparison against single-flank milling using a barrel tool is also fabricated. In particular, information technology is shown that surface roughness and manufacturing fourth dimension are significantly reduced when using double-flank machining with custom-shaped tool.
Surface roughness
Surface roughness is one of the primal parameters that influence a smooth movement between gears, their face-face contact, and consequently the life of the whole gear. Typically, the surface roughness is measured using a confocal microscope, still, due to the difficult accessibility of the faces of the gear, resin was applied in order to measure out a negative of the tooth space.
The process for obtaining the negative of the face proceeds as follows: first, the area to be measured is degreased with the DN1 degreaser cleaner provided by PLASTIFORM'south own company (PLASTIFORM, Madrid, Spain). Once this is done, a airtight area must be formed such that the fluid (liquid resin) covers both sides of the cavity, and then the fluid is applied to the measuring expanse using a dispensing gun. Finally, cca 6 min is needed for the solution to dry out, so one can remove the negative of the cavity, come across Fig. viii.
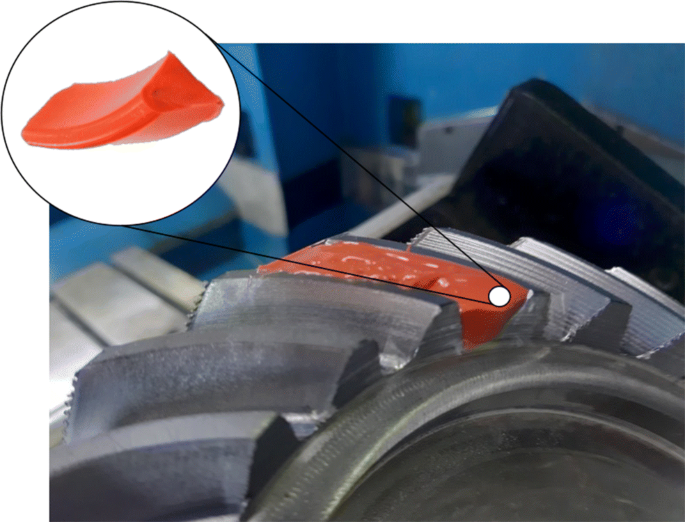
Curing procedure of the resin and its zoomed-in office later hardening
Information technology was selected a fluid type resin, so that it could menses through the unabridged gear cavity and thus adapt well to the surface of the faces. Specifically, the F65 product was used, which allows a semi-flexible geometry to exist obtained, suitable for measurement by both contact measuring systems and optical measurement systems. The precision obtained with this resin is ± i μm.
A Leica DCM 3D confocal microscope was used to analyze the surface roughness of the resin. Both sides of the cavity were analyzed, as the amount of excess of textile was slightly different on each side after roughing. The adjustment of the roughness measurement in this case was a cutting length of 0.8 mm and an evaluation length of 4 mm, according to ISO 4288 [32]. Effigy 9 shows the topography and related data of both sides of the cavity.
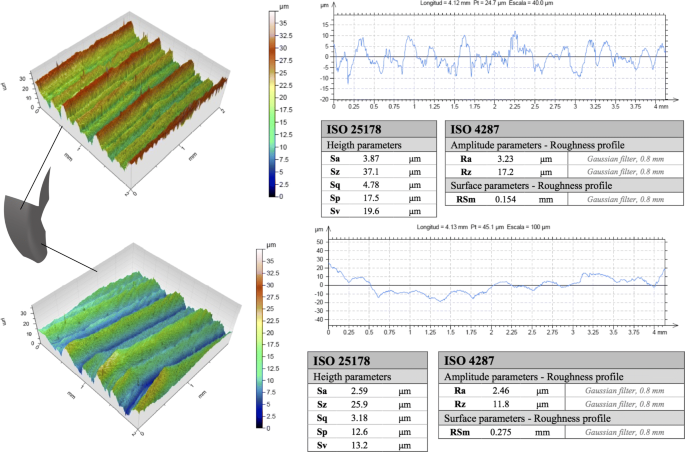
Surface expanse and contour roughness parameters values of the left (elevation) and correct (lesser) side of the gear tooth cavity
Topography on both sides of the molar cavity shows a perfectly recognizable grinding pattern, in which in that location are remarked peaks and valleys along the scanned surface caused past the random distribution of the abrasive grains. It is noticeable that slightly improve results in term of roughness were obtained on the right face, as the roughing operation leaves that face smoother and stepless between passes, merely the opposite of the left face up, as information technology can be seen in Fig. vii(d). However, this fact is non a limitation of the proposed double-flank arroyo, only it is due to the fact that the roughing stage left the right confront smoother.
The results are in accordance with "indicative surface roughness comparison" that many companies handle [33]. The roughness values obtained were adequate for a semifinishing operation considering they are shut to those obtained with similar strategies considering them as finishing operations.
Machining time
Some other aspect that was considered in this work was the analysis of machining time during semifinishing operations on gear teeth. To this end, machining time of ball end milling operation and double-flank SAM strategy with a custom-shaped tool was measured, and barrel flank milling virtual machining time was calculated. The conventional semifinishing operation using a ball stop manufactory with 4 mm bore was used with a stepover of 0.33 mm of depth of cutting in 3 lateral steps in each confront and a feed of 2800 mm/min. On the left face up, 20 axial passes were repeated three times axially (lx passes total) while on the right face 20 passes were sufficient. In contrast, semifinishing using a custom-shaped tool was accomplished in a single sweep with the following parameters: a feed of 500 mm/min and a spindle speed of 16000 rpm. In the example of single-flank milling using a barrel-shaped tool with 12 mm of barrel diameter, in total 20 passes were done to cover the whole surface with a feed of 848 mm/min.
With the above-mentioned values of cutting parameters for the three manufacturing semifinishing operations, the post-obit machining time results were obtained: (i) conventional ball finish milling: 2 min and 7 south, (2) double-flank SAM semifinishing with the custom-shaped tool: 24 south, and (iii) butt flank milling: 1 min and 8 s. Double-flank SAM dominated in terms of machining time. When comparison with the other ii, in the case of ball end milling, the semifinishing machining fourth dimension was reduced by 81.i%, saving in full 43 min per gear. In the case of barrel flank milling, SAM double-flank machining was 2.83 times faster than butt flank milling. See Fig. four for the summary of the machining times of each particular stage.
Dimensional deviation
Dimensional deviation of the three tested semi-finishing strategies: ball stop mill operation, double-flank SAM with a custom-shaped tool, and barrel flank milling were qualitatively compared. Figure 10 shows simulation results of the three semifinishing operations using a commercial software.
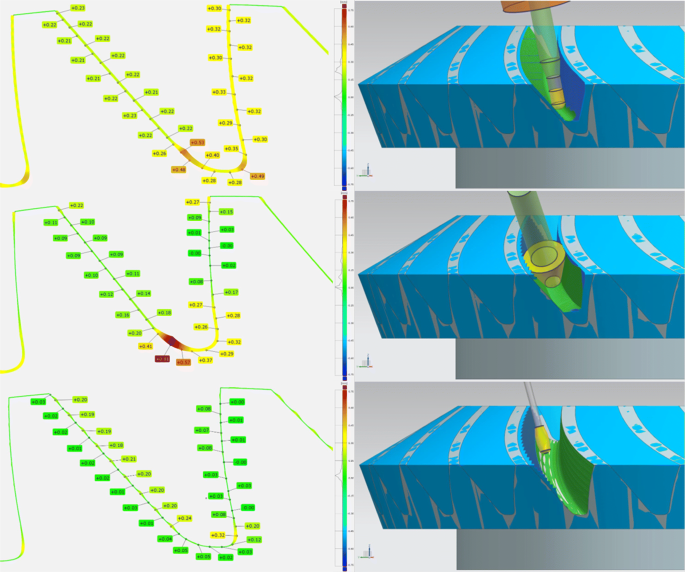
Dimensional deviation of the iii about faux semi-finishing strategies: Ball end manufacturing plant operation (height), double-flank SAM with a custom-shaped tool (eye), and barrel flank milling (bottom). The fault distribution along the tooth space (left column) and the imitation paths (right cavalcade) are shown
In the instance of the root surface of the molar, the results obtained past all methods were very similar, reaching a tooth surface excess of material of upwards to 0.8 mm. The results obtained on the tooth face surface show clear differences. In the case of ball finishing functioning, a uniform terminate was obtained along the entire surface with a stock around 0.23 mm. In the case of the SAM, at that place are two clearly differentiated zones. In the first zone, the correct face, the values obtained in the semi-finishing are practically close to the final geometry of the slice. On the left side, an undercut of 0.1 mm was obtained along the molar face. Comparing the to a higher place-mentioned results with barrel flank milling, it can be seen that the trouble on the root surface is virtually solved, except for the fillet radius, where is a stock of more than 0.3 mm. However, in the rest of the surface there is an undulation contour that goes from 0.03 mm in the lesser to 0.21 mm in the meridian.
Word and limitations
The proposed arroyo significantly reduces the semifinishing time past using a properly designed custom-shaped tool. The tool has to be manufactured in accelerate, however, the custom-shaped tool costs are low, in detail: cylindrical steel bar F115 (85€ ) to create 4 SAM tools, i.e., 21.25€ per the steel core of the tool, and 45€ to add the abrasive grains. In total, the price of the custom-shaped tool is 66.25€. In contrast, the on-market tool for ball cease milling, VF4SVBR0200, costs 120€.
The surface roughness values range Sa = 2.59–3.87 mm using the SAM approach which is a slightly more than the numbers that can be obtained by means of conventional milling [33]. Nevertheless, these values are acceptable in the case of a workpiece which later undergoes finishing operations.
Some other slight limitation is that the very bottom of the cavity is not attainable with the tool whose shape is designed to double-flank the ii faces of the cavity. The bottom of the cavity has to be machined using brawl end milling approach.
Comparing SAM double-flank machining with flank milling with barrel tools, both approaches offer similar accurateness, but double-flank machining is faster (factor of 2.83) due to the fact that only a single sweep of the tool is needed.
The presented results are promising, still, the double-flank methodology has been tested on one specific blazon of a screw bevel gear, with parameters shown in Table 2. For gears with apartment (planar) teeth, the double-flank approach is not challenging every bit the ideal move boils downward to a aeroplane-aeroplane bisector computation. The other extreme of small and even more curved reference geometry such as, e.chiliad., pinions has not been experimented with, simply tin be a promising venue for hereafter inquiry.
Conclusion and future work
We take presented a new variant of 5-axis flank machining, chosen double-flank. In this machining methodology, non simply the machining path, but as well the shape of the tool itself are the unknowns in an optimization-based framework. The numerical simulations received in [11] have been validated by physical manufacturing of a steel screw bevel gear. A custom-shaped SAM tool was designed and created for this purpose and applied in the semifinishing stage. The physical results confirmed the results obtained in the simulation stage, namely that the machining error gets reduced, the surface roughness is inside a standard range, and most remarkably, the machining time of the semifinishing stage is reduced past gild of magnitude when compared to ball end milling. When compared to flank milling with a barrel tool, the machining time is reduced by factor 2.83. These are very promising results towards future evolution of double-flank machining every bit a standard manufacturing technology.
As a future research we aim to farther develop this methodology and focus on other geometries, eastward.grand., blades and screw rotors, that seem to be well-suited for double-flank milling methodology using custom-shaped tools. Another research thread can get towards milling every bit the concept of double-flank methodology is not express simply to annoying tools, but could likewise be used for cut tools with flutes.
References
-
Krumme W (1967) Klingelnberg–Spiralkegdräder (Klingelnberg Spiral Bevel Gears) (in High german). Springer, New York
-
Zhang Z, Vocal Y, Xu C, Guo D (2012) A novel model for undeformed nanometer chips of soft-brittle hgcdte films induced by ultrafine diamond grits. Scr Mater 67(ii):197–200
-
Fuentes-Aznar A, Ruiz-Orzaez R., Gonzalez-Perez I. (2017) Numerical approach for decision of crude-cutting automobile-tool settings for fixed-setting face-milled screw bevel gears. Mech Mach Theory 112:22–42
-
Stadtfeld HJ (2014) Gleason Bevel Gear Technology: The Science of Gear Engineering and Modern Manufacturing Methods for Athwart Transmissions Gleason Works
-
Watson HJ (2013) Modern gear product. Elsevier, New York
-
Deng X-Z, Li G-G, Wei B-Y, Deng J (2014) Face-milling spiral bevel gear molar surfaces by application of 5-centrality CNC machine tool. Int J Adv Manuf Technol 71(5-8):1049–1057
-
Álvarez Á, Calleja A, Ortega N, De Lacalle L (2018) 5-centrality milling of big screw bevel gears: toolpath definition, finishing, and shape errors. Metals 8(5):353
-
Suh SH, Jih WS, Hong Hd, Chung DH (2001) Sculptured surface machining of spiral bevel gears with CNC milling. Int J Mach Tools Manuf 41(6):833–850
-
Gibson I, Rosen DW, Stucker B et al (2014) Additive manufacturing technologies, vol 17. Springer, New York
-
Bo P, Bartoň M (2019) On initialization of milling paths for 5-axis flank CNC machining of costless-class surfaces with general milling tools. Comput Aided Geom Des 71:thirty–42
-
Bo P, González H, Calleja A, De Lacalle LNL, Bartoň Chiliad (2020) five-axis double-flank CNC machining of spiral bevel gears via custom-shaped milling tools—part I Modeling and simulation. Precis Eng 62:204–212
-
Machchhar J, Plakhotnik D, Elber One thousand (2017) Precise algebraic-based swept volumes for arbitrary costless-form shaped tools towards multi-axis CNC machining verification. Comput-Aided Des
-
Bo P, Bartoň M, Plakhotnik D, Pottmann H (2016) Towards efficient five-centrality flank CNC machining of free-form surfaces via fitting envelopes of surfaces of revolution. Comput Aided Des 79:1–11
-
Li C, Bedi Southward, Mann S (2008) Flank millable surface design with conical and barrel tools. Comput-Aided Des Appl v:461–470
-
Zhang Z, Huang S, Wang S, Wang B, Bai Q, Bi Z, Kang R, Guo D (2017) A novel approach of high-performance grinding using developed diamond wheels. Int J Adv Manuf Technol 91 (9):3315–3326
-
Zhang Z, Cui J, Wang B, Wang Z, Kang R, Guo D (2017) A novel approach of mechanical chemic grinding. J Alloys Compd 726:514–524
-
Zhang Z, Huo F, Zhang X, Guo D (2012) Fabrication and size prediction of crystalline nanoparticles of silicon induced past nanogrinding with ultrafine diamond grits. Scr Mater 67(7-viii):657–660
-
Zhang Z, Guo D, Wang B, Kang R, Zhang B (2015) A novel arroyo of loftier speed scratching on silicon wafers at nanoscale depths of cut. Sci Rep five(i):1–nine
-
Zhang Z, Bo W, Kang R, Zhang B, Guo D (2015) Changes in surface layer of silicon wafers from diamond scratching. Cirp Register 64(i):349–352
-
Litvin FL, Fuentes A (2004) Gear geometry and applied theory. Cambridge University Press, Cambridge
-
Müller H, Thomas J (2007) Face-off: face hobbing vs. confront milling. Gear Solutions five(54):49–60
-
Klocke F, Brumm Thou, Staudt J (2014) Quality and surface of gears manufactured past gratis grade milling with standard tools. In: Proceedings of the international gear conference, Lyon, French republic, pp 26–28
-
Álvarez Á, Calleja A, Ortega N, De Lacalle L (2018) 5-axis milling of big spiral bevel gears: toolpath definition, finishing, and shape errors. Metals 8(5):353
-
Zhuang W, Hua L, Han X, Zheng F (2017) Design and hot forging manufacturing of non-circular spur bevel gear. Int J Mech Sci 133:129–146
-
Álvarez Á, Calleja A, Arizmendi Chiliad, González H, De Lacalle LL (2018) Spiral bevel gears face roughness prediction produced past CNC stop milling centers. Materials 11(8):1301
-
Yang X-Y, Tang J-Y (2014) Research on manufacturing method of CNC plunge milling for spur face-gear. J Mater Process Technol 214(12):3013–3019
-
Klocke F, Brumm Chiliad, Staudt J (2014) Quality and surface of gears manufactured by free form milling with standard tools. In: Proceedings of the international gear conference, Lyon, French republic, pp 26–28
-
Wilk West, Tota J (2008) Mod technology of the turbine blades removal machining Proc. of the* 8th Int. Conf. "Avant-garde manufacturing Operations", Scientific reports, pp 347–355
-
González HB, Calleja AO, Pereira OMN, Ortega NR, López de Lacalle LNM, Barton K (2018) Super abrasive machining of integral rotary components using grinding flank tools
-
Steel composition. https://virgamet.com/18hgm-18crmo4-1-7243-18cd4-708m20-15crmo4-example-hardening-steelhttps://virgamet.com/18hgm-18crmo4-1- https://virgamet.com/18hgm-18crmo4-i-7243-18cd4-708m20-15crmo4-case-hardening-steel7243-18cd4-708m20-15crmo4-example-hardening-steel
-
Aspinwall DK, Soo SL, Curtis DT, Pall AL (2007) Profiled superabrasive grinding wheels for the machining of a nickel based superalloy. CIRP annals 56(1):335–338
-
DIN EN ISO 4288 (1996) Geometrical product specifications (gps)—surface texture: Contour method: Rules and procedures for the cess of surface texture
-
Surface finish ranges and tolerances. https://www.cnccookbook.com/surface-end-chart-symbols-measure-calculators/
Funding
Open Access funding provided thanks to the CRUE-CSIC agreement with Springer Nature. The first author has been supported past Universidad del País Vasco (predoctoral grant PIF 19/161). The second author has been partially supported past the National Natural Science Foundation of People's republic of china (Grant No. 61672187 and No. 62072139). The fifths author has been partially supported by Spanish Ministry building of Science, Innovation and Universities: Ramón y Cajal with reference RYC-2017-22649 and PID2019-104488RB-I00. The remaining authors were supported by the European Wedlock's Horizon 2020 research and innovation programme under understanding No. 862025 and by the Elkartek funding program, grant no. KK-2020/00102, and too by PDC2021-121792-100 and PID2019-109340RB-100 projects.
Author information
Affiliations
Corresponding author
Ethics declarations
Ideals approval
The authors confirm that there are no ethical issues related to this paper.
Consent for publication
If accepted, the authors requite their consent to the journal to publish and further distribute the commodity co-ordinate to the journal policies.
Conflict of interest
The authors declare no competing interests.
Boosted information
Data availability
The data (the shape of the tool + its move), as a part of European Union's Horizon 2020 projection, will be available on the project homepage.
Code availability
The source may undergo other IP issues (e.g., patenting) and volition therefore not be publicly bachelor.
Consent to participate
All the authors are aware of beingness co-authors and gave their consents.
Publisher's note
Springer Nature remains neutral with regard to jurisdictional claims in published maps and institutional affiliations.
Rights and permissions
Open Access This commodity is licensed under a Creative Commons Attribution iv.0 International License, which permits utilize, sharing, adaptation, distribution and reproduction in any medium or format, as long as you give appropriate credit to the original author(s) and the source, provide a link to the Creative Commons licence, and point if changes were fabricated. The images or other tertiary party material in this article are included in the article'southward Creative Commons licence, unless indicated otherwise in a credit line to the material. If material is not included in the commodity'due south Creative Eatables licence and your intended apply is not permitted by statutory regulation or exceeds the permitted use, you will need to obtain permission straight from the copyright holder. To view a copy of this licence, visit http://creativecommons.org/licenses/by/4.0/.
Reprints and Permissions
Near this article
Cite this article
Escudero, G.Chiliad., Bo, P., González-Barrio, H. et al. five-axis double-flank CNC machining of spiral bevel gears via custom-shaped tools—Part II: physical validations and experiments. Int J Adv Manuf Technol 119, 1647–1658 (2022). https://doi.org/10.1007/s00170-021-08166-0
-
Received:
-
Accepted:
-
Published:
-
Issue Date:
-
DOI : https://doi.org/10.1007/s00170-021-08166-0
Keywords
- 5-axis CNC machining
- Double-flank machining
- Custom-shaped tools
- Semifinishing operations
- Tangential movability
- Free-form shape manufacturing
DOWNLOAD HERE
Bevel Gear Cutting Blade Geometry Inspection Pdf Scholar UPDATED
Posted by: samreld1972.blogspot.com
Comments
Post a Comment